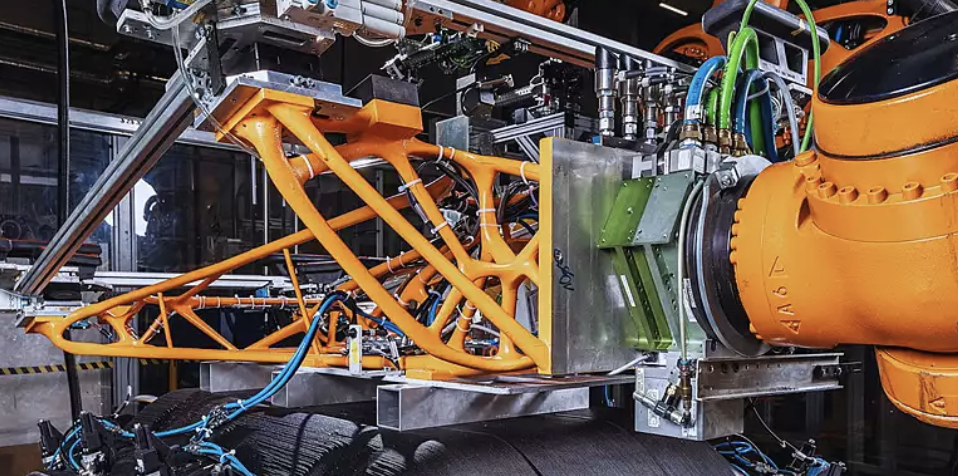
宝马集团正试图提升3D打印技术在定制机器人夹持器方面的应用,并推行到其广泛的生产网络中。这一创新举措能够创造快速、经济和多功能的优势,加强和优化整个制造流程和效率。
宝马集团的兰茨胡特工厂特别引进了一种革新型的仿生夹持器,这种夹持器在轻量化设计上取得了显著突破。这款专为处理CFRP车顶而设计的工具,相较于其前代产品,它成功减轻了25%的重量。该夹持器融合了选择性激光烧结(SLS)和大规模打印(LSP)技术,同时采用再生材料,使得其二氧化碳排放量与传统方法相比减少了约60%。
宝马集团慕尼黑工厂也采纳了一种创新的仿生夹持器,这款夹持器能够轻松处理BMW i4的完整地板组件。这种新型夹持器采用了一种独特的技术,即利用液态铝填充砂型铸造模具进行生产,其重量比传统型号轻了30%。这一显著的轻量化设计使得工厂能够使用更小、更轻的机器人,进而减少了能源消耗,并有助于降低二氧化碳的排放。宝马集团慕尼黑工厂的工厂工程和机器人技术主管Markus Lehmann对此表示:“在处理整个BMW i4地板组件时,我们成功地将夹持器的重量减轻了30%(即50公斤),这不仅提升了我们设备的使用寿命,也显著提升了生产效率。”
宝马集团对增材制造的投入并非仅限于机器人夹持器领域。公司在奥伯施莱斯海姆的增材制造园区已成为3D打印技术研究、生产和培训的重要基地。仅在2023年,该园区就成功生产了超过300,000个零件,而宝马的全球生产网络,包括斯巴达堡工厂和亚洲的各个工厂,也生产了100,000个零件。
此外,宝马集团多年来一直积极运用基于砂子的3D打印技术来制造原型铸件和大规模生产部件的模具。这种技术通过逐层铺设并粘合薄层沙子,然后注入液化铝来创建复杂的结构,为宝马的制造过程带来了显著的革新和效率提升。
在兰茨胡特轻质建筑技术中心,3D打印技术也被广泛应用于制造用于CFRP屋顶的大型机器人夹持器。这些夹持器重量约为120公斤,但仅需22小时即可完成生产,极大地缩短了生产周期,提高了生产效率。