2024年“新质生产力”成为新闻头条上的高频关键词。
什么是新质生产力?新质生产力到底出现在哪里?
自2023年5月28日以来,C919大飞机已经安全飞行超过1万小时,执行商业航班超过3700班次,承运旅客突破50万人次。作为中国首款按照国际通行适航标准自行研制、具有自主知识产权的喷气式中程干线客机。
C919在研制过程中攻克了100多项重大技术难关,尤其是机身外围和机翼曲面复合材料的精细化打磨,这直接关系到C919大飞机的执飞安全。
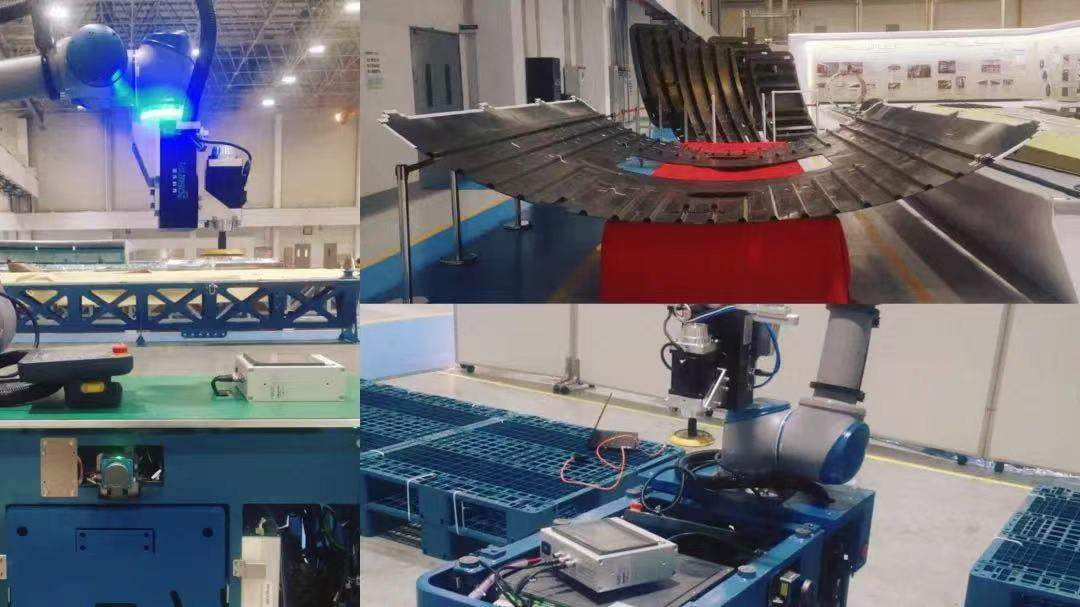
新能源电池盒去毛刺
盾构机在国家大基建层面被象征为“国之重器”,它代表着国家地下施工装备制造水平的最高标志,是衡量一个国家基建实力的重要标志之一。从20世纪90年代至今,国内盾构机已经从完全依赖进口逐渐发展成为占据了全球市场的七成份额,全球盾构机领域的领军者。如今,国产盾构机主体部分,如盾体、刀盘等重要零部件精细化打磨工艺,均为国内自主研发。2024年,全球最大直径高铁盾构机“领航号”下线正式开启穿越长江的掘进之旅。
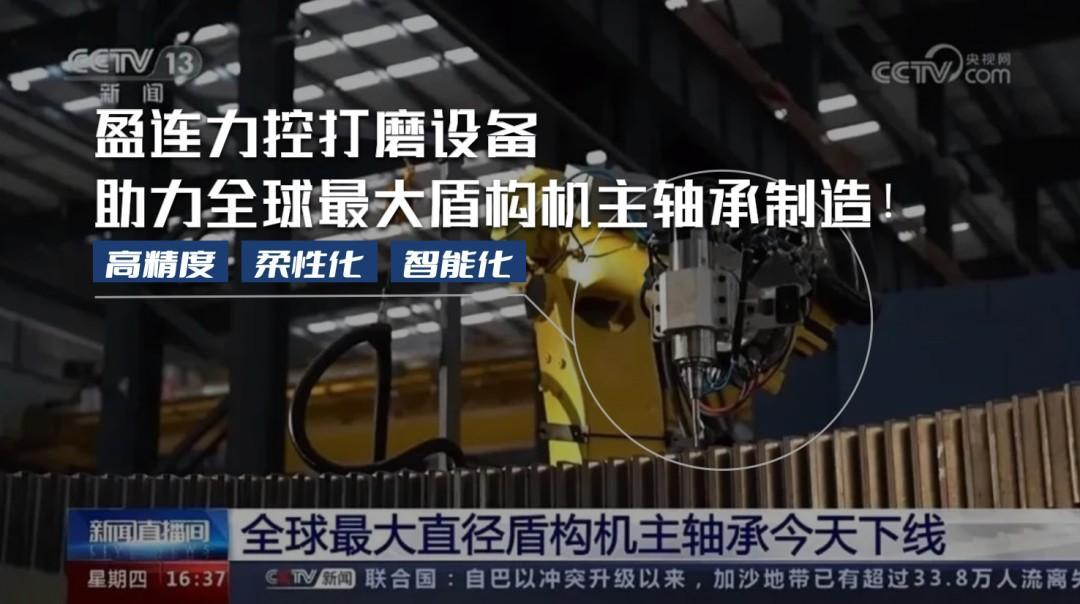
这些“新质生产力”技术的背后,都离不开国内一家名叫“盈连科技”的企业。作为机器人抛磨领域国产设备厂商的领军者,盈连科技致力于提供机器触觉感知与控制系统及力控解决方案的研发与生产,其主动柔顺力位补偿功能,144次/秒极速响应,0.7N高精度力度控制以及复杂凹凸面自适应能力,使其能够满足打磨行业全部的应用场景,在力控打磨领域处于技术领先地位,突破了国外的技术壁垒。
▍年销量20%增幅 想要吃透抛光打磨机器人百亿市场难点在哪儿?
工业制造是国民经济的基石,尤其是工业制造当中的高精密加工设备。抛光打磨作为工业制造领域中的关键环节,是一道不可或缺的程序。从国产盾构机、C919大飞机、轮船动力螺旋桨叶片,到汽车外观内饰,从发动机到尾气管,从3C电子到家用电器、从人工关节到电解金属,但凡高质量的产品都离不开抛光打磨这道工艺。
根据智研咨询的数据显示,2023年我国抛光打磨机器人市场规模仅为114.5亿元。目前盈连科技已经突破了行业的重点难点,解决的精准力控股及响应速度的难点。中国抛光打磨机器人销量年均增速将保持在20%左右,未来将是千亿级的市场。
我国工业化起步较晚,制造业的抛光打磨工序严重依赖于打磨工人,用工成本高,品控难以保证,且打磨工人流动性大,噪音和粉尘问题也是打磨工人职业病的罪魁祸首。随着人口老龄化加剧,打磨工人数量也在急剧锐减。部分工厂甚至月薪3万以上,招不到一个抛光打磨成手,抛光打磨领域的自动化转型已经迫在眉睫。
那么自动化打磨到底难在哪呢?首先由于在抛光打磨之前需经历多道工序,来料的不一致性特别高,导致机器人没办法很好的贴合工件表面作业。其次有别于码垛、焊接这种单点作业方式,抛光打磨作业是一种连续接触工件的场景。如果控制不好力,在工具接触的首次着力,就会造成工件或机械臂的损伤。相当于靠机械臂直接带着电机耗材去作业,通过不断挤压耗材变形来逐步调试工艺,将严重依赖工程师经验。而加装了力控设备,通过精准设定接触力的方式,有效解决了这个痛点。
从整体来看,打磨是一个非常非标的作业场景,目前打磨行业自动化水平不足10%,行业严重缺乏标准。不同客户之间差异化需求大,且客户对于误差容忍度低,尤其是3C数码类精细化电子元器件加工场景,客户对定位的精准度、力控稳定性、速度等方面有非常严格的要求。
▍盈连科技参与国家重大工程建设 解决行业难点痛点问题
由于准入技术门槛较高,我国力控打磨行业尚处非完全竞争状态,但在重点细分领域,国内企业在综合技术指标上已经能够对标欧美第一梯队。
在国产C919大飞机制造过程当中,国内头部力控打磨企业盈连科技凭借其专业的技术能力和严谨的技术方案,承担了C919复合材料表面打磨处理工作。据资料显示,C919大型客机采用了大量复合材料,其用量占全机结构总重的比例达11.5%。其中T800级高强碳纤维复合材料被应用于后机身和平垂尾等受力较大的部件的设计当中。玻璃纤维复合材料则应用于雷达罩以及襟翼等受力较小的部件。而芳纶蜂窝材料则应用于C919的舱门和客货舱地板。
不同材料之间的表层的密度不同,面对机舱曲面结构时,盈连科技力控系统通过力位补偿器内置压力传感器、位移传感器及姿态倾角传感器,实时感知机器人末端的位置姿态以及打磨工具与工件之间的接触状态。而嵌入式ARM芯片能够对输入信号进行高速处理,实时输出控制值对高精度电气比例阀进行控制,从而调整打磨工具的位置和力度。值得一提的是,力位补偿器采用重力补偿技术,可以在任何姿态下保证位移和力值的精确匹配,避免因重力影响而产生的误差。在执行C919机舱曲面结构打磨作业时,盈连科技打磨精度达到最小0.7N标准,解决了先进复合材料曲面高精度高质量的打磨要求。
齿圈倒角通常应用于盾构机主驱动系统的齿轮齿圈部分,在核心材料加工过程中控制倒角半径、倒角角度对于盾构机的性能有重要影响。2024年全球最大直径高铁盾构机“领航号”正式下线,该盾构机总长128米,总重约4000吨,刀盘直径15.4米,盈连科技凭借其自主研发的主动柔顺力控打磨系统,成功助力全球最大直径盾构机主轴承的制造。
与传统打磨材料程序不同,齿圈倒角除曲面结构外,在齿轮部分呈现齿状规则结构,盈连科技通过搭载的FDC力控系统对齿圈倒角的复杂凹凸面自适应,该套系统可实现双工艺自动控制、打磨特征点识别、打磨轨迹规划、工件/工具匹配度识别等功能。此外,FDC力控系统支持实时响应,速度达到144次/秒,最快达到了1-1200N快速响应。由于是一套独立的系统,跟机器人连接时无需二次开发,能够满足即插即用的效果,方便且易部署。通过部署机器人力控打磨系统,盈连科技将打磨效率提升了2.5-3倍,圆满完成盾构机主轴承齿圈倒角的高精度打磨作业。
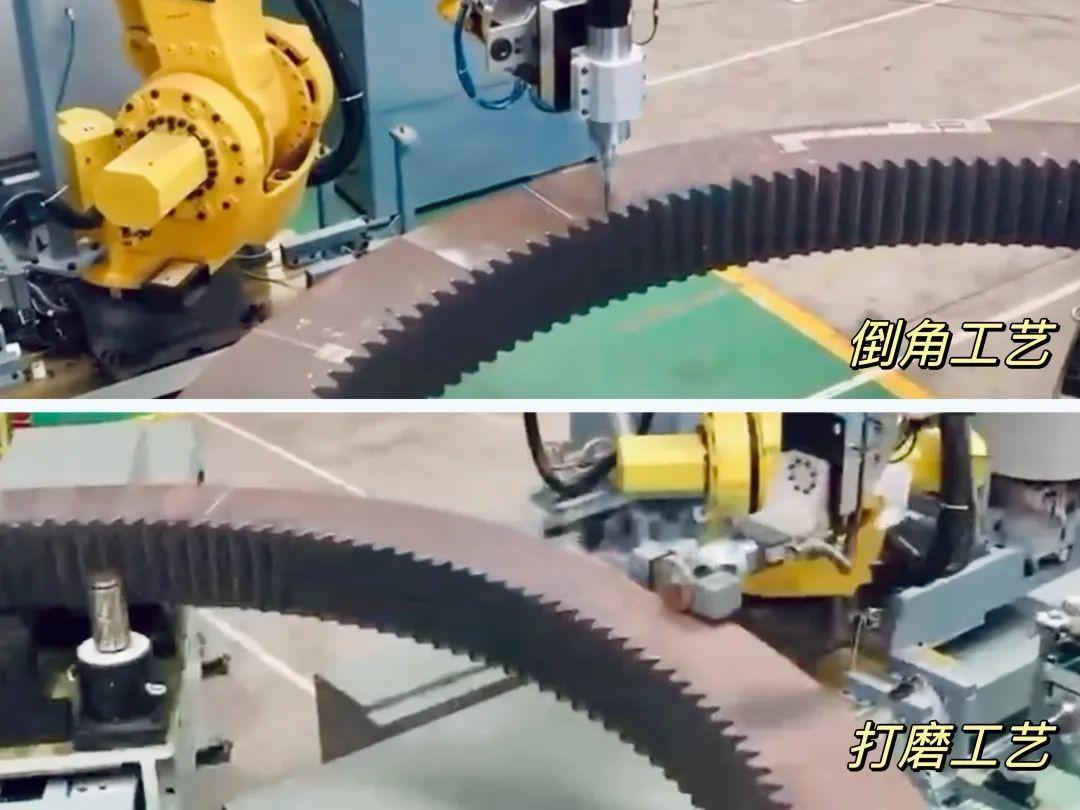
新能源汽车是国内制造业的主力军,相关数据显示,2024年1-9月,国内新能源汽车产销分别完成831.6万辆和832万辆,同比分别增长31.7%和32.5%,新能源汽车产业继续保持强劲的增长势头。而在汽车制造环节过程当中,新能源汽车最重要的电池仓部分则采用高强度塑料材质,来减轻车重以及提升绝缘和耐腐蚀性,每一台新能源车在出厂之前,都需要对高强度塑料电池仓进行去毛刺打磨,之后塞入动力电池进行封装。
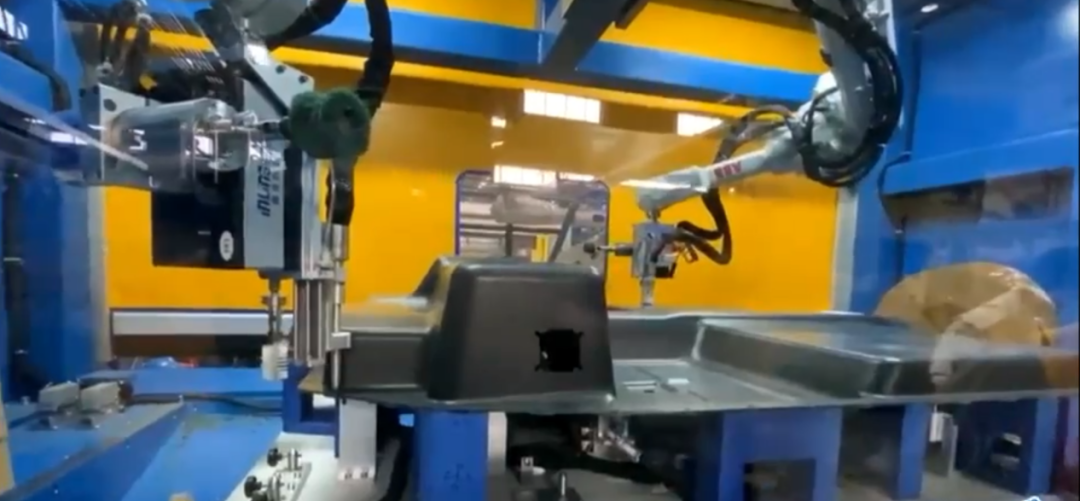
塑料电池仓精细化去毛刺打磨
为了更好定制塑料电池仓精细化去毛刺打磨方案,盈连科技为汽车客户打造了整体工作站解决方案,通过精准控制打磨余量,保护托盘表面的平整度和一致性,满足电池盒托盘对气密性的严格要求。同时针对电池仓的曲面结构部分,通过主动柔顺力位补偿功能解决复杂曲面结构的高精度打磨难题,确保打磨质量的一致性和效率。目前,盈连科技高精度打磨方案已获得比亚迪、宁德时代、祥鑫、大众、宝马多家企业认可,并建立长期合作关系。
除大型工业制造场景外,盈连科技力控打磨解决方案也适配于小型抛光打磨作业,如木质箱体表面打磨、小提琴面板表面打磨,3C笔记本铝制软金属打磨,碳纤维板或支架打磨,塑料件打磨等。
目前盈连科技还推出了自动打磨一体站,不仅可实现多道打磨工序一站操作,一体站还可以储存大量的工艺数据,集尘防爆,24小时不间断作业,相当于为客户输出了完整的解决方案,相当于客户贴身的工艺工程师。真正做到降本增效,操作便捷。
▍结语与未来:
面对年复合增长率20%的抛光打磨机器人市场,可以预见的是,在高端装备国产替代的要求下,盈连科技通过主动柔顺力控打磨系统,将核心技术打包在客户的解决方案当中,保证客户对于不同材料的打磨品质,加速客户的投入回本周期,为客户带来长期价值。
资料显示,盈连科技在2023年全年实现了逆势增长,其在力控打磨领域的出货量攀升至国内榜首,并服务超800余家行业客户,累计近2000例打磨工艺数据,稳步实现进口替代。目前盈连科技力控打磨方案已满足80%以上场景应用的快速部署,并且能够实现曲面自适应、重力补偿、恒力打磨等丰富功能,从而已经在中车、富士康、广汽等多个头部客户项目中应用,并参与了多个国家级重点项目。未来也将布局更多的机器人末端产品,真正做到全场景应用。
目前盈连科技拥有全国首家打磨测试中心,通过模拟真实生产环境中的打磨场景,对打磨工具、耗材以及工艺参数进行全面测试和验证。此外,盈连科技还与清华大学、南工程、合工大等30多所高校建立打磨实验室,并与FANUC、安川、埃斯顿、珞石、钱江、遨博、大族等20余家机器人厂商共建产业生态模块,帮助行业客户实现降本增效,通过“新质生产力”推动制造业的智能化转型升级。